There are various types of bearing grease, including lithium, polyurea, aluminum complex, marine, calcium, and wheel bearing greases. These greases are formulated with different properties and are suitable for specific applications.
Understanding the different types of bearing grease can help in selecting the appropriate lubricant for various bearing and machinery needs. Bearing grease is crucial for the proper functioning and longevity of bearings, and selecting the right type of grease is essential for optimal performance.
Different types of bearing grease offer varying properties such as water resistance, high-temperature resistance, and load-carrying capacity. This diversity allows for the selection of grease that matches the specific requirements of different applications, ensuring smooth and efficient operation of bearings. Let’s delve into the various types of bearing grease to understand their unique characteristics and applications.
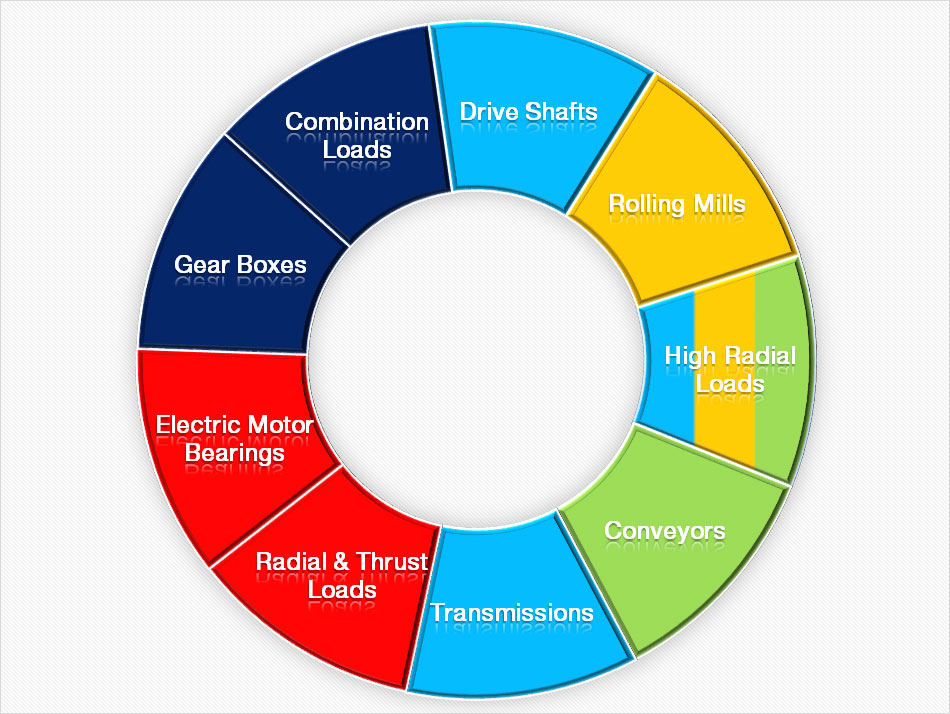
Credit: www.steelshieldtech.com.hk
Introduction To Bearing Grease
Different types of bearing grease include lithium, polyurea, aluminum complex, marine, calcium, and sodium thickener. Each type offers unique properties based on the thickeners, additives, and base oils used. It’s important to select the right grease for specific applications to ensure optimal bearing performance and longevity.
Bearing grease plays a crucial role in the smooth operation and longevity of various machinery components. It acts as a lubricant to reduce friction between moving parts, preventing wear and tear.
Role In Reducing Friction
- Bearing grease reduces friction between moving parts.
- It prevents wear and tear on machinery components.
- Helps in maintaining optimal performance and efficiency.
Importance Of Proper Selection
- Proper selection of bearing grease is vital for machinery longevity.
- Choosing the right grease ensures smooth operation and reduced maintenance costs.
- Incorrect grease selection can lead to increased friction and component failure.
Breaking Down Grease Components
Base Oils Explained
Base oils are the primary component of bearing grease, providing lubrication and reducing friction between moving parts. The most commonly used base oils include mineral oils, synthetic oils, and vegetable oils. Mineral oils are derived from crude oil and are cost-effective, while synthetic oils offer superior performance and stability. Vegetable oils, such as rapeseed and sunflower oil, are biodegradable and environmentally friendly.
Additives And Their Functions
Grease additives are essential for enhancing the performance and longevity of the grease. Antioxidants are added to prevent oxidation and extend the shelf life of the grease, while anti-wear additives form a protective layer on metal surfaces, reducing wear and tear. Other additives, such as corrosion inhibitors and extreme pressure additives, are included to protect bearings from rust and handle heavy loads.
Understanding Thickeners
Thickeners are crucial in determining the consistency and stability of bearing grease. Metallic soaps, such as lithium, calcium, and aluminum complex, are the most common thickeners used in grease production. Each type of thickener has unique properties, with lithium providing excellent water resistance, calcium offering good pumpability, and aluminum complex ensuring high-temperature performance.
Common Types Of Bearing Grease
Lithium Grease
Lithium grease is a popular choice due to its versatility and ability to withstand high temperatures.
Calcium Grease
Calcium grease is known for its water resistance and is commonly used in applications exposed to moisture.
Polyurea Grease
Polyurea grease is recognized for its excellent oxidation resistance and stability over a wide temperature range.
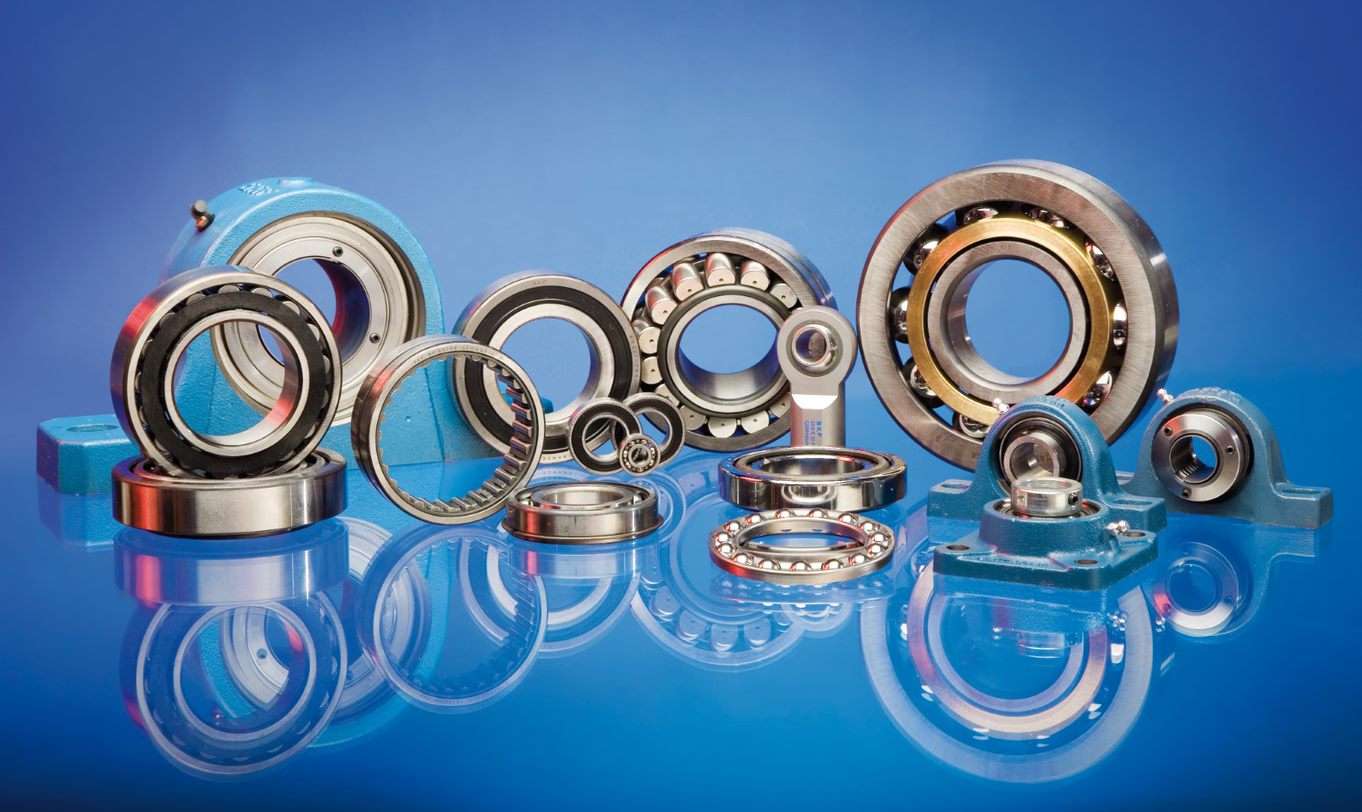
Credit: eriks.com
Specialty Greases For Specific Applications
Specialty greases are specifically formulated to meet the demanding requirements of various applications, providing superior performance and protection. These greases are designed to excel in specific conditions, such as high temperatures, marine environments, and food processing facilities. Understanding the different types of specialty greases and their unique properties is essential for selecting the right grease for a particular application.
High-temperature Greases
High-temperature greases are designed to withstand extreme heat and prevent oil separation, ensuring continued lubrication in applications such as industrial ovens, kilns, and automotive components. These greases typically contain additives that enhance thermal stability and oxidation resistance, allowing them to maintain their lubricating properties at elevated temperatures.
Marine Greases
Marine greases are formulated to withstand the harsh conditions encountered in marine environments, including exposure to saltwater and the presence of contaminants. These greases provide excellent water resistance and corrosion protection for bearings, bushings, and other components on boats, ships, and offshore equipment.
Food-grade Greases
Food-grade greases are specifically developed for use in food processing and pharmaceutical facilities where incidental contact with food or pharmaceuticals may occur. These greases are required to meet strict regulatory standards and are formulated using non-toxic ingredients to ensure the safety of the processed products. They provide effective lubrication while complying with food safety regulations.
Industry-specific Greases
Industry-specific greases are designed to meet the unique lubrication requirements of specific sectors, ensuring optimal performance and longevity of machinery and equipment. Whether it’s automotive applications, heavy-duty industrial machinery, or marine environments, tailored greases are formulated to withstand the specific operating conditions and demands of each industry.
Automotive Greases
Automotive greases are specially formulated to lubricate various components within vehicles, including wheel bearings, chassis parts, and suspension systems. These greases are engineered to withstand high temperatures, heavy loads, and challenging environmental conditions commonly encountered in automotive applications. Common types of automotive greases include lithium, calcium, and polyurea greases, each offering unique properties tailored to specific automotive lubrication needs.
Heavy-duty Industrial Greases
Heavy-duty industrial greases are designed to lubricate machinery and equipment operating in demanding industrial environments. These greases are formulated to provide exceptional protection against extreme pressures, high temperatures, and heavy loads. They are commonly used in applications such as manufacturing plants, mining operations, and construction equipment. Heavy-duty industrial greases often feature advanced additives and thickeners to ensure reliable lubrication and equipment performance.
Grease Selection For Wheel Bearings
Synthetic Vs Mineral Oil-based Grease
Synthetic greases offer better performance in extreme conditions.
Mineral oil-based greases are cost-effective and widely used.
Criteria For Choosing The Right Grease
- Operating temperature: Ensure the grease can withstand the wheel’s operating temperature.
- Load capacity: Select a grease that can handle the specific load requirements.
- Water resistance: Opt for a grease that provides protection against water ingress.
- Longevity: Choose a grease with a suitable service life for wheel bearings.
Lubrication Methods For Bearings
Bearing grease is essential for reducing friction and wear between moving parts in industrial machinery. Proper lubrication extends the lifespan of bearings and ensures smooth operation. There are various lubrication methods available, each with its own advantages and considerations. Understanding the different lubrication methods for bearings is crucial for maintaining optimal performance and preventing premature failure.
Manual Lubrication Techniques
Manual lubrication techniques involve the application of grease to bearings by hand or using simple tools such as grease guns or brushes. This method allows for precise control over the amount and location of grease applied, making it suitable for equipment with specific lubrication requirements. However, manual lubrication requires regular maintenance and monitoring to ensure consistent and adequate lubrication.
Automatic Lubrication Systems
Automatic lubrication systems, also known as centralized lubrication systems, deliver grease to bearings at regular intervals through automated dispensing units. These systems are designed to provide consistent and metered lubrication, reducing the risk of over- or under-lubrication. Automatic lubrication systems are ideal for large and complex machinery, as they help to minimize downtime and ensure uniform lubrication across multiple bearings.
Maintenance And Grease Reapplication
Proper maintenance and regular reapplication of grease are essential for ensuring optimal performance and longevity of bearings. Understanding the signs of grease deterioration and following best practices for re-lubrication are key in this process.
Symptoms Of Grease Deterioration
- Change in color or consistency
- Increased operating temperature
- Unusual noise or vibration
- Visible contamination or wear
Best Practices For Re-lubrication
- Clean the bearing housing before re-greasing
- Use the correct type and amount of grease
- Follow manufacturer’s guidelines for reapplication intervals
- Monitor grease condition regularly
- Implement proper sealing mechanisms
Environmental Considerations
When it comes to bearing grease, it’s crucial to consider its impact on the environment. Two key factors to focus on are biodegradability and the effect of grease on ecosystems.
Biodegradable Greases
- Biodegradable greases are formulated to break down naturally over time.
- They are designed to minimize harm to the environment.
- These greases typically have a lower ecological footprint.
Impact Of Grease On Ecosystems
- Grease can contaminate soil and water sources if not properly managed.
- It may harm plants, animals, and aquatic life in ecosystems.
- Proper disposal and usage can mitigate negative environmental impacts.
Navigating Manufacturer Recommendations
Manufacturers’ recommendations for bearing grease types include lithium, polyurea, aluminum complex, marine, calcium, and wheel bearing grease. Each type offers unique properties based on the thickeners, base oils, and additives used, catering to specific applications and operating conditions. When navigating these recommendations, it’s crucial to consider factors such as temperature, load, and environmental conditions to select the most suitable bearing grease.
Navigating Manufacturer Recommendations When it comes to selecting the right type of bearing grease, it can be overwhelming to navigate through the different options available. One of the most important factors to consider is the manufacturer’s recommendations for the specific application. This ensures that the grease will perform optimally and help extend the life of the bearings. Interpreting Specifications Before choosing a bearing grease, it’s essential to interpret the specifications provided by the manufacturer. These specifications include the type of thickener, base oil viscosity, and NLGI grade. The type of thickener determines the compatibility with other greases and the operating temperature range. The base oil viscosity affects the grease’s lubricating ability, while the NLGI grade determines the stiffness of the grease. When to Follow or Deviate While it’s essential to follow the manufacturer’s recommendations, there may be situations where deviation is necessary. For example, if the application operates at a higher temperature than the recommended range, it may be necessary to select a grease with a higher temperature range. However, it’s crucial to consult with the manufacturer or a lubrication expert before deviating from the recommended grease. Types of Bearing Grease There are different types of bearing grease available, each with unique properties and suitable for specific applications. These include: – Lithium Grease: Suitable for general-purpose applications, including chassis and wheel bearings. – Polyurea Grease: Suitable for high-temperature applications, including electric motor bearings. – Aluminium Complex Grease: Suitable for heavy-duty applications, including mining and construction equipment. – Calcium Grease: Suitable for low-speed, high-load applications, including conveyor systems. – Marine Grease: Suitable for marine applications, including boat trailer wheel bearings. – Sodium Grease: Suitable for high-speed applications, including automotive wheel bearings. – Synthetic Grease: Suitable for extreme-temperature applications, including industrial ovens. Navigating through the different types of bearing grease can be challenging. However, by understanding the manufacturer’s recommendations, interpreting the specifications, and selecting the appropriate grease, you can ensure optimal performance and extend the life of the bearings.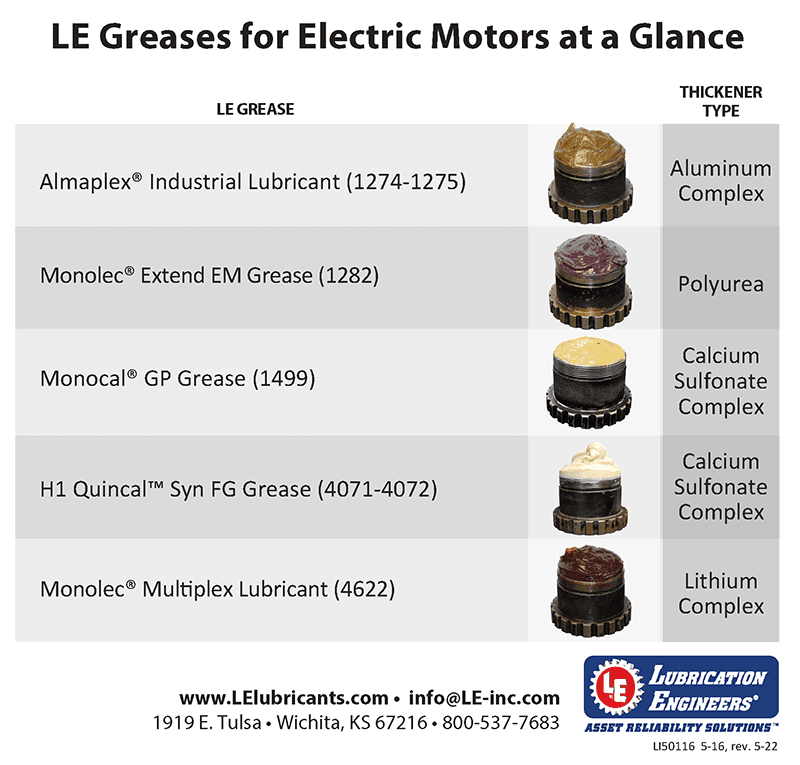
Credit: lelubricants.com
Frequently Asked Questions
How Many Types Of Bearing Grease Are There?
There are several types of bearing grease, including lithium, polyurea, aluminum complex, marine, calcium wheel bearing, and oil/sodium thickener. These greases can be classified as multipurpose (MP) greases, extreme pressure (EP) greases, heavy-duty greases, specialty greases, automotive greases, industry greases, etc.
The classification depends on the unique properties of base oils, additives, and thickeners used in the process. Greases are primarily classified by their thickeners, and the most common type of thickener is metallic soap.
What Grease Should Be Used On Bearings?
Select a suitable grease for bearings based on the type: Lithium, aluminum complex, marine, calcium, or polyurea.
How To Identify Grease Types?
To identify grease types, focus on the thickeners used, such as metallic soaps, bentonite clay, silica gel, polyurea, and inorganic thickeners. Soap-based greases typically consist of three main ingredients.
What Is The Difference Between #1 And #2 Grease?
#1 and #2 grease differ based on their thickener composition and intended applications in machinery.
Conclusion
Selecting the right type of bearing grease is crucial for ensuring the optimal performance of bearings. With the availability of different types of bearing grease, it can be overwhelming to choose the right one. However, by understanding the unique properties of the base oils, additives, and thickeners used in the process, you can make an informed decision.
Whether you need multipurpose, marine, heavy-duty, specialty, or automotive grease, ensure that you consider the manufacturer’s recommendations and the specific needs of your application.