When choosing high-temperature bearing grease, consider the operating temperature, load, and speed. Also, check compatibility with the bearing materials.
High-temperature bearing grease selection is crucial for optimal equipment performance. It involves considering factors like operating temperature, load, and speed, as well as compatibility with bearing materials. By choosing the right grease, you can enhance equipment reliability, minimize downtime, and prolong bearing life.
Additionally, selecting a high-quality grease can result in improved equipment performance and reduced maintenance costs. It’s essential to consider these factors to ensure the proper functioning of machinery in high-temperature environments.
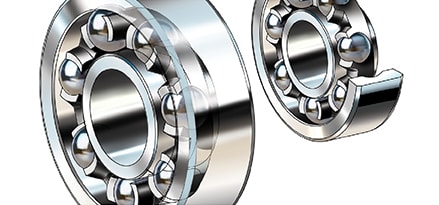
Credit: www.mobil.com
High Temperature Bearing Grease Essentials
Choosing the right high temperature bearing grease is essential for optimal performance. Consider factors such as temperature range, frequency of greasing, and compatibility with the application. It’s crucial to select a grease with the appropriate base oil, thickener technology, and additive composition to ensure reliable lubrication in high temperature environments.
High Temperature Bearing Grease Essentials When it comes to choosing the right high temperature bearing grease, there are several key properties to consider. Understanding these properties can help you select the best grease for your application and ensure optimal bearing performance. Key Properties: 1. Temperature Range: The temperature range of the grease is one of the most critical properties to consider. High temperature greases are designed to withstand extreme temperatures, typically ranging from 150°C to 260°C. It is important to ensure that the grease you choose is suitable for the operating temperature of your application. 2. Viscosity: The viscosity of the grease is another important property to consider. The viscosity should be appropriate for the application and the operating temperature. Greases that are too thin may not provide adequate lubrication, while greases that are too thick may cause excessive drag and heat generation. 3. Base Oil: The base oil in the grease should be carefully selected based on the operating temperature, load, and speed of the application. Synthetic oils are often used in high temperature greases because they provide better resistance to oxidation and thermal breakdown. 4. Additives: Additives are often used in high temperature greases to improve their performance in specific applications. For example, anti-wear additives can help protect bearings from wear and extend their service life. Common Applications: High temperature greases are used in a wide range of applications, including: 1. Automotive: High temperature greases are used in automotive applications such as wheel bearings, chassis parts, and constant velocity joints. 2. Industrial: High temperature greases are used in industrial applications such as bearings in steel mills, paper mills, and kilns. 3. Aerospace: High temperature greases are used in aerospace applications such as landing gear bearings, flap actuator bearings, and engine accessory bearings. In conclusion, choosing the right high temperature bearing grease is critical to ensuring optimal bearing performance and minimizing downtime. By considering key properties such as temperature range, viscosity, base oil, and additives, and understanding common applications, you can select the best grease for your specific needs.Assessing Your Needs
Identifying Operating Conditions
Before choosing high-temperature bearing grease, identify the specific operating conditions such as temperature, speed, and load.
Understanding Bearing Requirements
Understand the specific requirements of your bearings to select the appropriate grease that can withstand high temperatures and provide optimal lubrication.
Temperature Ranges And Grease Selection
When it comes to selecting high-temperature bearing grease, understanding the appropriate temperature ranges is crucial. The right grease can ensure optimal performance and longevity of bearings in extreme conditions.
Defining High Temperature
High temperature refers to environments where conventional greases may fail, typically above 120°C.
Acceptable Temperature Range For Greases
Greases must operate within specific temperature ranges to maintain their lubricating properties effectively.
Grease Type | Temperature Range |
---|---|
Conventional Lithium Grease | -20°C to 120°C |
High-Temperature Synthetic Grease | 120°C to 200°C |
Extreme-Temperature Ceramic Grease | 200°C to 1000°C |
When choosing grease for high-temperature applications, consider the operating temperature, bearing speed, and load for optimal performance.

Credit: www.machinerylubrication.com
Base Oil And Thickener Types
When selecting high-temperature bearing grease, it is crucial to consider the base oil and thickener types. These factors play a significant role in determining the performance and suitability of the grease for specific applications.
Selecting Base Oil Viscosity
The base oil viscosity is a critical consideration when choosing high-temperature bearing grease. It determines the lubricating ability of the grease at elevated temperatures. Higher viscosity oils are suitable for heavy loads and high operating temperatures, while lower viscosity oils are ideal for lower temperatures and lighter loads.
Thickener Technology And Stability
The thickener type and stability are equally important when selecting high-temperature bearing grease. Different thickener technologies offer varying degrees of stability and performance at elevated temperatures.
Thickener Type | Properties |
---|---|
Lithium Complex | Excellent high-temperature performance and mechanical stability |
Calcium Sulfonate | Outstanding water resistance and corrosion protection |
Aluminum Complex | Superior thermal and oxidative stability |
Each thickener type offers unique advantages, and the choice depends on the specific requirements of the application.
Additives And Their Impact
When selecting high-temperature bearing grease, it’s crucial to understand the role of additives and their impact on the performance and longevity of the grease. Additives play a significant role in enhancing the properties of the grease, ensuring it performs optimally under extreme conditions.
Role Of Additives
Additives in high-temperature bearing grease are essential for improving its resistance to oxidation, corrosion, and wear. They enhance the load-carrying capacity and prevent metal-to-metal contact, thereby reducing friction and extending the bearing’s lifespan.
Compatibility With Bearings
Additives must be carefully chosen to ensure compatibility with the specific type of bearings and operating conditions. Different types of additives are used for various bearing materials, such as steel, ceramic, or hybrid bearings, to provide tailored protection and performance.
Environmental Considerations
When choosing high-temperature bearing grease, it is crucial to consider various environmental factors that can impact the performance and longevity of the lubricant. Environmental considerations play a significant role in ensuring the proper functioning of bearings in demanding conditions.
Ambient Conditions
Ambient conditions refer to the surrounding environment in which the bearings operate. Factors such as temperature fluctuations, humidity levels, and exposure to external elements can affect the performance of high-temperature bearing grease.
Contamination Risks
Contamination risks involve the potential exposure of the grease to foreign particles, water, chemicals, or other contaminants that can degrade the lubricant and compromise the bearing’s functionality. It is essential to assess and mitigate contamination risks to maintain optimal performance.
Performance Factors
When choosing high temperature bearing grease, consider factors like the acceptable temperature range, lubrication needs, and base oil selection. Proper grease selection is crucial for high temperature performance and can impact the longevity of bearings and applications. Additionally, understanding the composition, operating temperature, and relubrication intervals is essential for optimal grease performance.
Load Carrying Capacity
The load carrying capacity of high-temperature bearing grease is crucial in ensuring optimal performance and longevity of the bearings. It determines the maximum load that the grease can withstand without causing excessive wear or failure.
Speed Tolerance
Speed tolerance refers to the ability of the grease to maintain its lubricating properties at varying speeds. It is essential to choose a high-temperature bearing grease that can withstand the rotational speeds of the application without compromising performance.

Credit: www.carterbearings.co.uk
Maintenance And Relubrication
To ensure optimal performance of high temperature bearings, it is crucial to select the right grease. Consider factors such as oil type, viscosity, thickener stability, and operating temperature when choosing high temperature bearing grease. Proper selection and relubrication intervals are key for preventing overheating and premature wear.
Establishing Relubrication Intervals
One of the critical factors in maintaining high-temperature bearings is establishing relubrication intervals. Grease lubrication is essential for bearings to function properly and extend their lifespan. However, over-greasing or under-greasing can lead to bearing failure. Therefore, it is crucial to determine the appropriate relubrication frequency for high-temperature bearings.Grease Application Techniques
Proper grease application techniques are necessary to ensure that the lubricant reaches all critical areas of the bearing. The most common methods of grease application include manual, automatic, and centralized lubrication systems. Manual lubrication requires a trained operator to apply the grease using a grease gun, while automatic systems use a pump to deliver grease to the bearing at a predetermined interval. Centralized lubrication systems are ideal for large industrial applications, where multiple bearings require lubrication at once. In summary, maintaining and relubricating high-temperature bearings is critical to extend their lifespan and prevent costly downtime. Establishing the appropriate relubrication intervals and using proper grease application techniques are essential factors in maintaining high-temperature bearings. By following these guidelines and selecting the right high-temperature bearing grease, you can ensure the optimal performance of your bearings, even in extreme temperature conditions.Manufacturer And Industry Recommendations
When it comes to choosing high-temperature bearing grease, seeking advice from manufacturers and industry experts is crucial for optimal performance and longevity.
Leveraging Expert Advice
Manufacturers often provide detailed recommendations on the types of high-temperature bearing greases that are suitable for specific applications. They can offer insights into the ideal viscosity, composition, and relubrication intervals based on the operating conditions of the equipment.
Case Studies And Best Practices
Studying case studies and industry best practices can provide valuable real-world examples of successful high-temperature bearing grease selection and application. By analyzing these scenarios, you can gain practical knowledge to make informed decisions for your own machinery.
Monitoring And Troubleshooting
When it comes to ensuring the optimal performance and longevity of high-temperature bearing grease, monitoring and troubleshooting play a crucial role. By being vigilant about the signs of grease failure, implementing preventive measures, and conducting regular assessments, you can effectively maintain the health of your bearings and prevent costly downtime.
Signs Of Grease Failure
Identifying the signs of grease failure is essential for preventing potential damage to bearings. Some common indicators include:
- Increased operating temperature
- Unusual noise or vibration
- Leakage or over-lubrication
- Visible discoloration or contamination
Preventive Measures
To mitigate the risk of grease failure, it’s imperative to implement preventive measures such as:
- Regular lubrication schedule
- Proper grease selection based on operating conditions
- Effective sealing to prevent ingress of contaminants
- Monitoring equipment for signs of overheating
Frequently Asked Questions
What Is The Best Grease For High Temperature Bearings?
For high temperature bearings, the best grease is one with a high-temperature rating and suitable thickener for extreme heat conditions.
How To Choose Bearing Grease?
To choose bearing grease, consider the acceptable temperature range, periodic or ongoing grease needs, base oil type and viscosity, thickener type, additive composition, ambient and operating temperature, atmospheric contamination, loading, speed, and relubrication intervals. Proper selection is crucial for high-temperature performance, bearing wear and failure prevention, and minimizing financial costs from repairs and downtime.
What Temperature Is Considered High Temperature Grease?
High temperature grease is considered to be effective at temperatures above 150 degrees Celsius.
Can Too Much Grease Overheat A Bearing?
Over-greasing a bearing can cause overheating due to grease degradation, leading to premature wear and failure.
Conclusion
Choosing the right high-temperature bearing grease is crucial for optimal performance and longevity. Consider factors like temperature range, base oil type, thickener technology, and relubrication intervals to make an informed decision. By selecting the appropriate grease, you can enhance the efficiency and durability of your bearings, minimizing the risk of premature wear and failure.