One common mistake when greasing bearings is under- or over-lubrication, which can lead to issues. Applying too little grease can shorten bearing life, while excess grease can cause heat build-up and other problems.
Proper lubrication is crucial to ensure optimal performance and longevity of bearings in industrial applications. Over-greasing or under-greasing can result in costly maintenance and downtime, highlighting the importance of following correct greasing procedures. By avoiding these common mistakes and using the right amount of grease, you can prevent premature wear and ensure smooth operation of bearings, ultimately improving the overall efficiency of machinery and equipment.
Introduction To Bearing Greasing
Common mistakes when greasing bearings include under- or over-lubrication, leading to premature wear and damage. Insufficient grease causes abrasion, while excess grease results in heat buildup and seal damage. Properly applying grease to bearings ensures optimal performance and longevity, preventing unnecessary downtime and maintenance issues.
Proper lubrication is crucial for the longevity and performance of bearings. However, greasing errors are common and can lead to significant consequences. In this blog post, we will discuss the five most common mistakes when greasing bearings and their impact on bearing performance.
Importance Of Proper Lubrication
Bearings operate under high pressure and friction, and proper lubrication is necessary to reduce wear and extend their lifespan. Bearings that are not adequately lubricated can experience harmful abrasion, leading to premature failure. Proper lubrication also helps to dissipate heat and prevent corrosion.
Consequences Of Greasing Errors
Greasing errors can have significant consequences on bearing performance. Adding too little lubricant can lead to bearing failure due to increased friction and wear. On the other hand, over-lubrication can cause excess heat buildup, seal damage, and increased downtime. Surplus grease in a bearing cavity can cause the rollers or balls to slide rather than turn, pushing and churning the grease out of the way. To avoid these issues, it is essential to follow proper greasing procedures and use the right amount of lubricant. It is also crucial to select the right type of lubricant for the specific bearing application. By avoiding these common greasing mistakes, you can ensure the longevity and optimal performance of your bearings.
Too Much Grease
When it comes to greasing bearings, applying too much grease is a common mistake that can lead to serious performance issues. Over-greasing can have detrimental effects on the functionality and lifespan of bearings, making it essential to understand the symptoms and impact of this error.
Symptoms Of Over-lubrication
Identifying the signs of over-lubrication is crucial in preventing potential damage to bearings. Some common symptoms include:
- Excessive grease leakage around the bearing housing
- Elevated operating temperatures due to excess friction
- Inefficient lubricant distribution within the bearing
How Over-greasing Affects Performance
Over-greasing can significantly impact the performance of bearings, leading to:
- Increased friction and heat generation
- Deterioration of bearing seals
- Potential clean-up challenges and extended downtime
- Compromised functionality due to rollers or balls sliding instead of turning “`
Insufficient Greasing
Risks Of Under-lubrication
Under-lubrication poses risks such as premature bearing failure, increased friction, and potential overheating.
Identifying Inadequate Lubrication
Common signs of inadequate lubrication include excessive noise, vibration, and visible wear on the bearing surfaces.
.webp)
Credit: www.slsbearings.com
Choosing The Wrong Grease
One common mistake when greasing bearings is under- or over-lubrication. Applying too little or too much grease can lead to premature bearing failure and increased friction, impacting performance and longevity. To prevent these issues, it’s essential to follow proper lubrication guidelines for optimal bearing function.
Impact Of Incorrect Lubricant Selection
Choosing the wrong grease for bearing lubrication can have detrimental effects on the performance and longevity of the bearings. When the incorrect grease is used, it can lead to increased friction, overheating, premature wear, and ultimately, bearing failure. This can result in costly downtime, maintenance, and replacement expenses for industrial machinery.
Tips For Selecting The Right Grease
When selecting the right grease for bearing lubrication, there are several factors to consider to ensure optimal performance and longevity of the bearings. Here are some tips to help you choose the appropriate grease:
- Consider the operating conditions, such as temperature, load, and speed, to determine the appropriate grease consistency and base oil viscosity.
- Refer to the bearing manufacturer’s guidelines and recommendations for compatible grease types and specifications.
- Ensure the grease compatibility with other lubricants and seals used in the equipment to prevent any adverse reactions.
- Regularly monitor the condition of the grease and perform grease analysis to detect any signs of contamination or degradation.
- Train and educate personnel on proper grease handling, application, and storage to avoid contamination and ensure effective lubrication.
Neglecting Bearing Cleanliness
Neglecting bearing cleanliness is a common mistake that can lead to premature bearing failure and costly downtime. When lubricating bearings, it’s essential to pay attention to the cleanliness of the bearing and its surrounding environment. Failure to maintain cleanliness can result in lubrication contamination issues, compromising the performance and lifespan of the bearing.
Lubrication Contamination Issues
Contaminants such as dirt, dust, and moisture can infiltrate the bearing housing, leading to abrasive wear and reduced lubricant effectiveness. Additionally, improper handling practices can introduce contaminants during the greasing process, further exacerbating the issue.
Maintaining Clean Lubrication Practices
To avoid lubrication contamination, it’s crucial to establish and maintain clean lubrication practices. This includes implementing proper storage and handling procedures for lubricants, as well as regularly cleaning the bearing housing and surrounding areas to prevent the ingress of contaminants.

Credit: www.bearing-news.com
Ignoring Manufacturer’s Specifications
One common mistake when greasing bearings is ignoring the manufacturer’s specifications. Applying too little or too much grease can lead to premature bearing failure and costly repairs. It’s essential to follow guidelines to ensure optimal performance and longevity of the bearings.
Following Oem Guidelines
Ignoring the manufacturer’s specifications when greasing bearings can lead to severe consequences. It is crucial to adhere to the OEM guidelines to ensure optimal performance and longevity of the bearings. Deviating from these specifications can result in premature wear and failure of the bearings.
Consequences Of Deviating From Specifications
When you ignore the manufacturer’s specifications for greasing bearings, you risk causing excessive heat buildup, seal damage, and increased downtime. Over-lubrication can lead to the rollers or balls sliding instead of turning, displacing the grease and affecting the bearing’s functionality. Under-lubrication, on the other hand, can result in harmful abrasion and a shortened bearing lifespan. It is essential to follow the OEM guidelines to prevent these detrimental outcomes.
Lubricating Based On Time Not Condition
Lubricating based on time rather than condition is a common mistake that can lead to premature bearing failure. By adhering to a set schedule for greasing bearings, rather than assessing their actual lubrication needs, the risk of over-lubrication, under-lubrication, or using the wrong type of grease increases significantly.
The Flaw Of Scheduled Maintenance
When greasing bearings based on a predetermined schedule, there is a tendency to either over-grease or under-grease them, leading to operational issues and reduced bearing lifespan. Over-greasing can result in excess heat build-up and seal damage, while under-greasing can cause harmful abrasion and premature wear.
Adopting Condition-based Lubrication
Condition-based lubrication involves monitoring the actual condition of the bearings and applying grease only when necessary. By utilizing techniques such as vibration analysis and thermal imaging, maintenance teams can determine the optimal timing for greasing, ensuring the right amount of lubricant is applied when needed, thereby prolonging bearing life and reducing the risk of costly downtime.
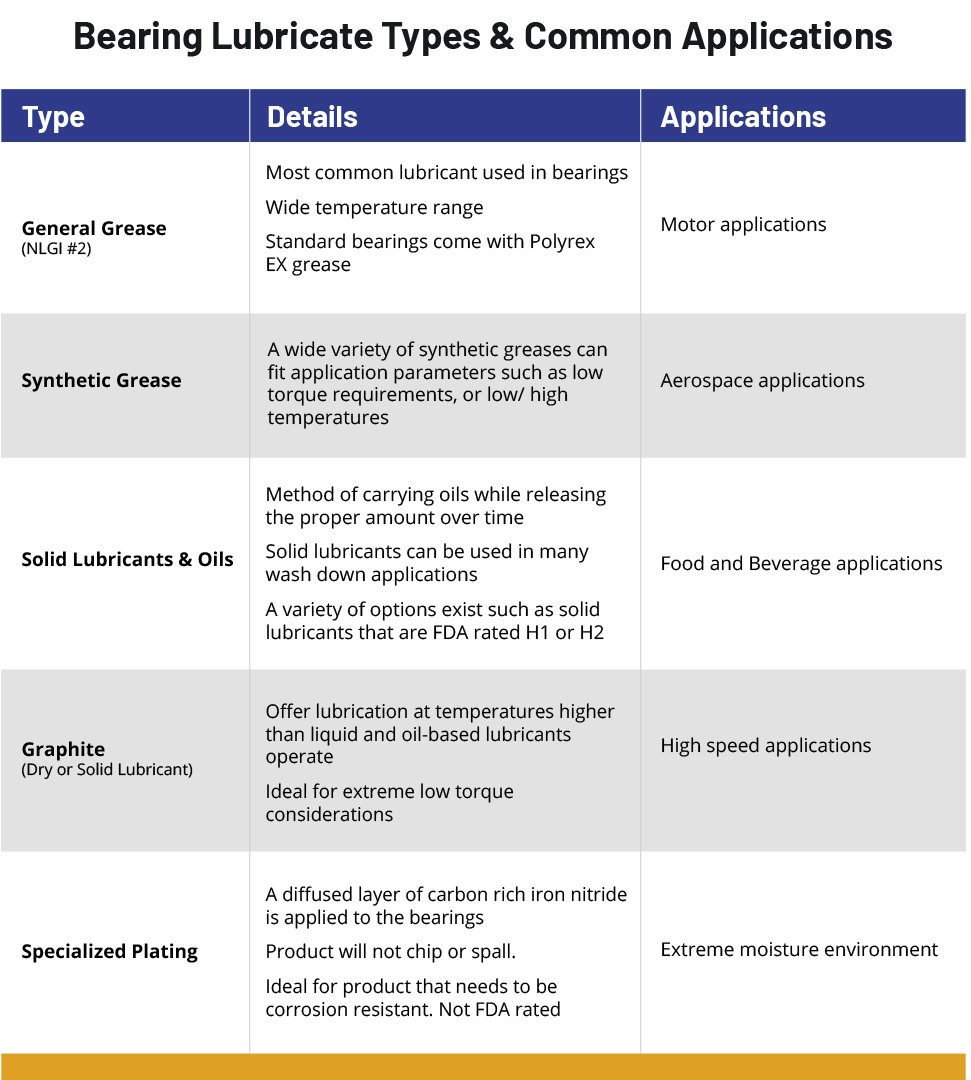
Credit: www.bdsbearing.com
Failing To Properly Displace Old Grease
When greasing bearings, failing to properly displace old grease is one of the most common mistakes. This can lead to excess heat build-up, seal damage, and increased downtime. To avoid this, introduce new grease in the center of the bearing to push out the old grease effectively.
Failing to Properly Displace Old Grease One of the most common mistakes made when greasing bearings is failing to properly displace old grease. When new grease is added without displacing the old grease, it can lead to a buildup of grease and leakage, ultimately causing damage to the bearing. Techniques for Effective Grease Replacement To avoid this mistake, there are several techniques that can be used for effective grease replacement. One effective technique is to use a bearing packer, which ensures that new grease is evenly distributed throughout the bearing. Another technique is to use a grease gun with a flexible hose attachment, which allows for easier access to the bearing. Avoiding Grease Build-up and Leakage In addition to properly displacing old grease, it is important to take steps to avoid grease build-up and leakage. One way to do this is to use the correct amount of grease for the bearing, as over-greasing can lead to excess grease build-up and leakage. It is also important to use the correct type of grease for the bearing, as using the wrong type can lead to compatibility issues and ultimately cause damage to the bearing. To summarize, when greasing bearings, it is important to properly displace old grease and take steps to avoid grease build-up and leakage. Using the correct techniques and tools, as well as the correct amount and type of grease, can help ensure that the bearing is properly lubricated and functioning at its best.
Preventive Measures And Best Practices
Proper greasing of bearings is essential for ensuring smooth operation and prolonging the lifespan of machinery. However, several common mistakes can hinder the effectiveness of the greasing process, leading to premature wear and tear of bearings. By understanding these mistakes and implementing preventive measures and best practices, maintenance professionals can optimize equipment performance and minimize downtime.
Implementing A Greasing Program
Implementing a structured greasing program is crucial for maintaining equipment reliability. This involves establishing a regular greasing schedule based on manufacturer recommendations and operational conditions. It’s important to use the right type and quantity of grease, and to ensure proper distribution to all bearing points. By adhering to a systematic greasing program, maintenance staff can prevent under or over-lubrication, which are common causes of bearing failure.
Training And Awareness For Maintenance Staff
Providing comprehensive training and raising awareness among maintenance staff is vital for avoiding greasing mistakes. Training programs should cover topics such as proper greasing techniques, identification of over-lubrication and under-lubrication symptoms, and the importance of following equipment-specific guidelines. Additionally, creating awareness about the impact of incorrect greasing practices on machinery performance can empower maintenance personnel to adhere to best practices and proactively identify potential issues.
Conclusion: Ensuring Bearing Longevity
Properly greasing bearings is crucial for their longevity, but there are several common mistakes to avoid. These include under or over-lubricating, applying grease unevenly, using the wrong type of grease, and not cleaning the bearing beforehand. By following proper greasing techniques, you can ensure your bearings last longer and operate more efficiently.
Summarizing Key Takeaways
When greasing bearings, common mistakes like under or over-lubrication can lead to premature wear and damage. It is crucial to follow proper lubrication techniques to ensure optimal bearing performance.
Encouraging Proactive Maintenance Culture
Establishing a proactive maintenance culture within your organization can help prevent common greasing mistakes. Regularly train maintenance personnel on correct lubrication procedures to prolong bearing longevity.
Frequently Asked Questions
What Is A Common Mistake When Greasing A Bearing?
The common mistake when greasing a bearing is adding too little or too much lubricant. This can lead to premature bearing failure due to lack of lubrication or excess heat build-up. It’s important to apply the right amount of grease for optimal bearing performance.
What Happens If You Over Lubricate A Bearing?
Over lubricating a bearing can lead to excess heat, seal damage, cleanup issues, and increased downtime. Excessive grease causes rollers to slide instead of turn, displacing the grease and causing problems.
Which Bearing Should You Not Lubricate?
Do not lubricate slow-moving bearings like tonearm or clock bearings, but use corrosion-resistant materials if running dry.
What Is The Proper Way To Grease A Bearing?
To properly grease a bearing, apply new grease in the center to push out the old grease. If that’s not possible, apply grease to one side and let the old grease escape from the other side. Avoid over-lubricating, which can cause excess heat and damage.
Conclusion
Proper bearing greasing is crucial to prevent issues like premature wear and excess heat. Avoiding common mistakes such as over-lubrication or under-lubrication is key for optimal bearing performance and longevity. By following best practices for greasing bearings, you can ensure smooth operation and extend the lifespan of your equipment.