The best grease for high load bearings is lithium complex grease with molybdenum disulfide. It offers excellent load-bearing capacity and durability.
High load bearings require specialized lubrication to perform optimally under intense pressure. Lithium complex grease with molybdenum disulfide is widely recommended due to its exceptional load-bearing properties. This type of grease provides superior protection against wear and extreme pressures. It also offers excellent thermal stability, ensuring the bearings operate smoothly even at high temperatures.
Proper lubrication extends the lifespan of bearings, minimizes downtime, and enhances overall machine efficiency. Choosing the right grease can significantly impact the performance and longevity of high load bearings. Therefore, investing in high-quality lithium complex grease with molybdenum disulfide is essential for heavy-duty applications.
Introduction To High Load Bearings
High load bearings are crucial in various industrial applications. These bearings support heavy loads and ensure smooth operations. Their role is critical in machinery and equipment.
Importance In Industrial Applications
High load bearings are essential in industries like manufacturing, construction, and mining. These industries use heavy machinery that relies on robust bearings. Without proper bearings, machinery can fail, causing downtime and financial loss.
Industry | Application |
---|---|
Manufacturing | Conveyor systems, presses |
Construction | Cranes, bulldozers |
Mining | Excavators, drills |
Challenges In Lubrication
Lubricating high load bearings presents unique challenges. Standard greases may not withstand the pressure and temperature. This can lead to bearing wear and failure.
Selecting the right grease is crucial. It must have high load-carrying capacity. High-temperature stability is also important. The grease should resist oxidation and provide long-lasting protection.
- High load-carrying capacity
- High-temperature stability
- Oxidation resistance
- Long-lasting protection
Understanding these challenges helps in choosing the best grease for high load bearings. Proper lubrication ensures the longevity and efficiency of industrial machinery.
Characteristics Of High-quality Grease
Choosing the best grease for high load bearings is crucial. High-quality grease ensures the bearings run smoothly and last longer. It prevents wear and tear under extreme conditions. Let’s dive into the key characteristics of such greases.
Viscosity And Consistency
Viscosity is the measure of a fluid’s resistance to flow. For high load bearings, the grease must have the right viscosity. It should be thick enough to stay in place but not too thick to cause resistance.
Consistency refers to how firm the grease is. It’s measured using the NLGI scale. A higher NLGI number means a thicker grease. High load bearings often need grease with an NLGI grade of 2 or 3. This ensures the grease stays put under heavy loads.
Characteristic | Requirement |
---|---|
Viscosity | Thick but not too thick |
Consistency | NLGI grade 2 or 3 |
Additives For Performance Enhancement
Additives are special ingredients added to grease. They enhance its performance. Common additives include anti-wear agents, extreme pressure additives, and corrosion inhibitors.
- Anti-wear agents: These reduce friction and wear between metal surfaces.
- Extreme pressure additives: These protect the bearings under heavy loads.
- Corrosion inhibitors: These prevent rust and corrosion, extending the life of the bearings.
Choosing grease with the right additives is essential. It ensures the bearings perform well under high load conditions.
Types Of Grease And Their Applications
Choosing the right grease for high load bearings is crucial. It ensures smooth operation and longevity. Different types of greases have specific properties suited for various applications. Here, we will explore three popular types of grease: Calcium Sulfonate Complex Grease, Polyurea Grease, and Lithium Complex Grease.
Calcium Sulfonate Complex Grease
Calcium Sulfonate Complex Grease is known for its excellent water resistance. It performs well under extreme pressure and high load conditions. This grease also offers superior protection against rust and corrosion.
Applications:
- Marine equipment
- Heavy-duty industrial machinery
- High-temperature applications
Polyurea Grease
Polyurea Grease is ideal for high-temperature environments. It provides excellent thermal stability and oxidation resistance. This grease is also known for its long service life and low noise characteristics.
Applications:
- Electric motors
- Automotive components
- High-speed bearings
Lithium Complex Grease
Lithium Complex Grease is versatile and widely used. It offers good mechanical stability and water resistance. This grease also provides excellent performance in a broad temperature range.
Applications:
- Automotive wheel bearings
- Industrial machinery
- General-purpose applications
Understanding the properties and applications of each type of grease helps in making an informed decision. Always choose the right grease for your specific needs to ensure optimal performance and longevity of your equipment.

Credit: www.machinerylubrication.com
Factors Determining Grease Selection
Selecting the best grease for high load bearings is crucial. Various factors influence this decision. Understanding these factors ensures optimal performance and longevity of the bearings.
Load And Speed Considerations
Load and speed significantly impact grease selection. High load bearings need grease that can withstand extreme pressure. The grease must also handle the speed of the bearing. Bearings operating at high speeds require grease with high shear stability.
Choosing the right grease ensures the bearing operates smoothly. This reduces wear and tear and extends the bearing’s life.
Temperature Ranges
Temperature is another critical factor. Bearings often operate in varying temperature conditions. The chosen grease must perform well in both high and low temperatures. Grease with a high dropping point is ideal for high temperatures. For low temperatures, the grease should maintain its consistency and not become too thick.
Temperature adaptability is essential for ensuring the grease provides consistent lubrication. This helps in preventing bearing failures due to temperature extremes.
Environmental Conditions
Environmental conditions play a significant role in grease selection. Bearings may be exposed to water, dust, and other contaminants. Grease with excellent water resistance and sealing properties is crucial. This prevents contamination and ensures the bearing remains protected.
Corrosion inhibitors in the grease also help in protecting the bearings. This ensures long-term reliability and performance, even in harsh environments.
Factor | Consideration | Importance |
---|---|---|
Load and Speed | High pressure and high shear stability | Ensures smooth operation and longevity |
Temperature | High dropping point and low-temperature consistency | Prevents bearing failures |
Environmental Conditions | Water resistance and corrosion inhibitors | Protects against contamination and harsh environments |
Performance Testing Of Grease
Finding the best grease for high load bearings requires thorough performance testing. This ensures the grease can withstand extreme conditions without breaking down. Various testing methods help assess the quality and durability of the grease.
Astm Test Methods
The American Society for Testing and Materials (ASTM) provides standardized methods for testing grease. These tests measure different properties of the grease.
- ASTM D2266: Measures wear protection.
- ASTM D2596: Tests load-carrying capacity.
- ASTM D1743: Assesses rust prevention.
- ASTM D3336: Evaluates high-temperature performance.
These tests help determine if the grease can protect bearings under high load conditions. Each test focuses on a specific property critical for high load bearings.
Field Performance Evaluations
Lab tests are crucial, but field performance evaluations provide real-world data. These evaluations involve using the grease in actual machinery and equipment.
Field tests consider:
- Operating temperatures
- Load conditions
- Environmental factors
Field tests help verify if the grease performs as expected under practical conditions. They also help identify any unforeseen issues that lab tests might miss.
Combining ASTM methods with field evaluations gives a comprehensive view of the grease’s capabilities. This approach ensures the grease chosen will perform well under high load conditions.
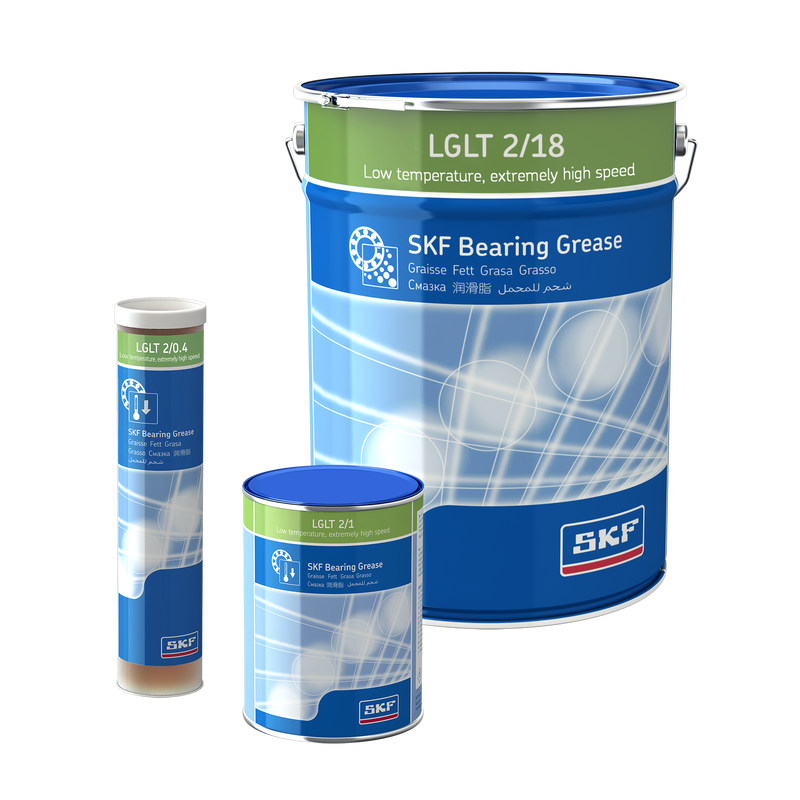
Credit: www.skf.com
Case Studies
Understanding the best grease for high load bearings is essential. Different industries have unique needs. Let’s explore some case studies. These examples show how the right grease improves performance.
Heavy Machinery
Heavy machinery operates under extreme conditions. Excavators, bulldozers, and cranes need robust lubrication. One study focused on a construction company. They used a calcium sulfonate complex grease. This grease reduced downtime by 20%. It also extended bearing life by 30%. The high load carrying capacity was crucial. It also provided excellent water resistance.
Here is a comparison of different greases used in heavy machinery:
Grease Type | Load Carrying Capacity | Water Resistance |
---|---|---|
Calcium Sulfonate Complex | High | Excellent |
Lithium Complex | Medium | Good |
Polyurea | Low | Poor |
Automotive Bearings
Automotive bearings face constant friction and high loads. A study in the automotive industry tested synthetic greases. A leading car manufacturer switched to a polyurea grease. This grease improved fuel efficiency by 5%. It also reduced bearing temperatures by 15%. The synthetic formula provided long-lasting performance. It also lowered maintenance costs significantly.
Benefits of using polyurea grease in automotive bearings:
- High-temperature stability
- Reduced wear and tear
- Improved fuel efficiency
Aerospace Applications
Aerospace bearings require precision. They operate in extreme conditions. One aerospace company tested a lithium complex grease. This grease handled high loads and extreme temperatures. It provided excellent corrosion protection. The study showed a 25% increase in bearing lifespan. It also reduced the frequency of maintenance checks.
Key features of lithium complex grease for aerospace:
- High load carrying capacity
- Temperature resistance
- Corrosion protection
Maintenance Tips For High Load Bearings
Maintaining high load bearings is essential for their longevity and performance. Proper maintenance ensures smooth operation and reduces the risk of failure. Below are some key tips to help you maintain your high load bearings effectively.
Proper Application Techniques
Proper application techniques are crucial for the longevity of high load bearings. Always use the correct amount of grease. Too much or too little can cause issues. Follow the manufacturer’s guidelines for application.
Use a clean, grease gun for application. Contaminants can damage the bearings. Ensure the bearing surfaces are clean before applying new grease.
Apply grease evenly. Uneven application can lead to poor performance and wear. Rotate the bearing while applying to ensure even coverage.
Re-lubrication Intervals
Re-lubrication intervals are vital for high load bearings. Regular re-lubrication keeps the bearings in top condition. Follow the manufacturer’s recommended intervals.
Consider the operating conditions. High temperatures or speeds may require more frequent lubrication. Keep a log of re-lubrication activities. This helps track and plan maintenance schedules.
Operating Condition | Re-lubrication Interval |
---|---|
Normal Load | Every 6 months |
High Load | Every 3 months |
Extreme Load | Monthly |
Monitoring And Troubleshooting
Monitoring and troubleshooting are essential to prevent unexpected failures. Regularly inspect the bearings for signs of wear or damage. Look for unusual noises or vibrations during operation.
Use temperature sensors to monitor the bearing temperature. An unusual increase in temperature can indicate a problem. Vibration analysis can also help detect issues early.
Keep an eye on the grease condition. Dark or contaminated grease indicates a need for re-lubrication. Address any issues promptly to avoid further damage.
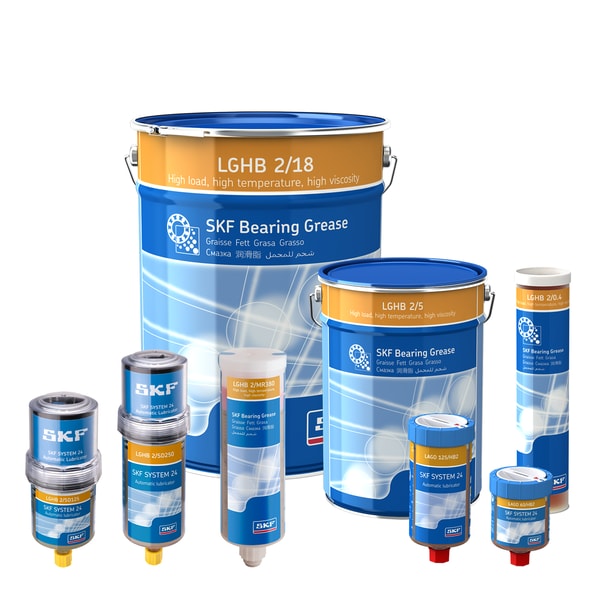
Credit: www.skf.com
Future Trends In Bearing Lubrication
The world of bearing lubrication is evolving rapidly. Innovations are driven by the need for better performance and sustainability. In this section, we will explore the latest trends shaping the future of bearing lubrication.
Synthetic Grease Developments
Synthetic greases are at the forefront of modern lubrication technology. They offer superior performance compared to traditional greases. With advancements in chemical engineering, new synthetic greases are being developed.
These greases can withstand higher temperatures and extreme pressures. They provide excellent protection for high load bearings. These attributes make them ideal for industrial applications.
A key benefit of synthetic greases is their longer lifespan. They reduce the need for frequent reapplication. This leads to cost savings and increased efficiency in operations.
Additionally, synthetic greases are designed to be more environmentally friendly. They produce less waste and have fewer harmful by-products.
Sustainability In Lubrication
The push for sustainability is influencing the field of lubrication. Manufacturers are focusing on creating eco-friendly lubricants. These lubricants aim to reduce environmental impact while maintaining performance.
Biodegradable greases are becoming more popular. These greases break down naturally without harming the environment. They are ideal for applications where contamination could be an issue.
Another trend is the use of renewable resources in lubricant production. Companies are sourcing raw materials from sustainable origins. This practice supports the global movement towards greener practices.
Additionally, there is a focus on reducing energy consumption in lubrication processes. Efficient lubricants can lower the energy required for machinery operation. This contributes to overall energy savings and reduces carbon footprints.
Type of Grease | Benefits | Applications |
---|---|---|
Synthetic Grease | High temperature resistance, Long lifespan, Environmentally friendly | Industrial machinery, Automotive, Aerospace |
Biodegradable Grease | Eco-friendly, Safe for contamination-prone areas | Agriculture, Marine, Food processing |
Frequently Asked Questions
What Is High Load Bearing Grease?
High load bearing grease is a specialized lubricant. It is designed to handle heavy loads and high pressure. It reduces friction and wear in bearings.
Why Use Grease For High Load Bearings?
Grease for high load bearings ensures optimal performance. It minimizes wear, reduces friction, and extends bearing life. It also prevents corrosion and contamination.
Which Properties Are Important In High Load Grease?
Key properties include high load-carrying capacity, excellent adhesion, and thermal stability. Resistance to water and contaminants is also crucial. These properties ensure reliable performance.
Can High Load Grease Reduce Maintenance Costs?
Yes, high load grease can reduce maintenance costs. It extends the life of bearings and reduces downtime. It also decreases the need for frequent re-lubrication.
Conclusion
Choosing the right grease for high load bearings is crucial. The right grease ensures longevity and efficiency. Always consider the specific requirements of your machinery. High-quality grease can prevent wear and reduce maintenance costs. Make an informed choice to keep your equipment running smoothly and reliably.