Ensure longer lifespan by following these bearing maintenance tips: Handle with care, check housing and shaft, mount correctly, avoid overheating, use proper tools, prevent corrosion, and ensure proper lubrication. Proper maintenance and inspection are crucial to prevent common bearing problems, improve reliability, productivity, and reduce operating costs of equipment.
Signs of bearing failure include squeaking, grinding noises, excessive vibration, increased noise, fatigue, and shortened service life. Common bearing failures result from overheating, contamination, inadequate lubrication, misalignment, corrosion, brinelling, electrical pitting, improper mounting, and bad fits. Prevent damage by addressing issues like misalignment, unbalance, looseness, and friction that can affect bearings.
Regular maintenance and inspections are essential for optimal bearing performance and longevity.
Introduction To Bearing Problems
Discover essential tips for maintaining bearings to ensure longevity. Handle with care, check housing, mount correctly, prevent overheating, use proper tools, avoid corrosion, and ensure proper lubrication. Regular maintenance and inspections can prevent common issues and improve equipment reliability and performance.
Bearings are essential components of machinery and equipment that facilitate smooth movement and reduce friction. However, like any other mechanical component, bearings are also prone to wear and tear, and if not maintained properly, they can fail prematurely. Bearing problems can cause significant downtime, loss of productivity, and ultimately lead to costly repairs or replacements.Common Causes Of Bearing Failure
There are several reasons why bearings fail, some of which include:- Overheating
- Contamination
- Inadequate lubrication
- Misalignment
- Corrosion
- Improper mounting
- Bad fits
Signs Of Impending Bearing Issues
It is essential to identify the signs of impending bearing problems before they cause significant damage. Some of the warning signs to look out for include:- Unusual noises, such as grinding, clicking, or squeaking
- Increased vibration or chatter
- Excessive heat or smoke
- Visible wear or damage to the bearing or surrounding components
- Changes in performance or efficiency
Quick Fixes For Bearing Issues
When dealing with bearing problems, it’s crucial to address them promptly to prevent further damage and ensure smooth operation. Quick fixes can help to temporarily alleviate bearing issues until a more thorough maintenance approach can be implemented.
Temporary Solutions For Noisy Bearings
Noisy bearings can be a nuisance and indicate potential problems. Here are some temporary solutions to address noisy bearings:
- Re-lubrication: Applying a suitable lubricant can help reduce noise temporarily.
- Adjustment: Checking for misalignment and making necessary adjustments can mitigate noise levels.
- Isolation: Isolating the bearing from excessive vibrations can help minimize noise.
Emergency Measures For Overheated Bearings
Overheated bearings require immediate attention to prevent severe damage. Emergency measures for overheated bearings include:
- Cooling: Ceasing operation and allowing the bearing to cool down can prevent further overheating.
- Cleanliness: Removing any debris or contaminants that may be contributing to the overheating.
- Proper Lubrication: Ensuring the bearing is adequately lubricated to reduce friction and heat generation.
Essential Bearing Maintenance Tips
When it comes to ensuring the smooth operation and longevity of machinery, bearing maintenance plays a crucial role. Proper maintenance not only prevents costly downtime but also enhances the overall efficiency of equipment. Here are some essential tips to keep your bearings in optimal condition.
Routine Inspection Protocols
Regular visual inspections are imperative to identify any signs of wear, misalignment, or contamination. This involves checking for unusual noise, vibration, or temperature fluctuations, which could indicate potential bearing issues.
Cleaning And Lubrication Best Practices
Cleaning the bearings before lubrication is essential to remove any dirt, debris, or old lubricant that may hinder optimal performance. Once cleaned, lubrication should be carried out using the appropriate lubricants in the correct quantities to minimize friction and wear.
Proper Handling And Storage
Handle bearings with care to prevent damage and ensure longevity. Proper maintenance includes checking housing, correct mounting, avoiding overheating, using the right tools, preventing corrosion, and ensuring proper lubrication. Regular inspections and maintenance can help avoid common bearing failures and improve equipment reliability and lifespan.
Proper handling and storage of bearings is crucial to ensure their optimal performance and longevity. Guidelines for Bearing Handling and Optimal Storage Conditions for Bearings must be followed meticulously to prevent damage and maintain efficiency.Guidelines For Bearing Handling
When handling bearings, always handle with care to prevent damage. Ensure to check the bearing housing and shaft for any irregularities. Mount the bearings correctly and avoid preheating or overheating them. Always use the proper tools to avoid any mishandling. To prevent corrosion, ensure proper lubrication of the bearings.Optimal Storage Conditions For Bearings
Proper storage is essential to maintain bearing quality. Store bearings in a clean, dry environment away from direct sunlight and moisture. Avoid storing bearings near sources of heat or cold. Keep bearings in their original packaging until ready for use to prevent contamination. Rotate older stock first to ensure proper inventory management. In summary, following these guidelines for handling and storage will significantly prolong the life and efficiency of bearings.Correct Installation Techniques
Proper installation of bearings is crucial for their optimal performance and longevity. By following step-by-step installation procedures and avoiding common errors, you can ensure that your bearings are installed correctly. Let’s take a closer look at the recommended installation techniques.
Step-by-step Installation
Installing bearings requires careful attention to detail. Here is a step-by-step guide to help you through the installation process:
- Prepare the work area: Clean the work surface and ensure it is free from debris or contaminants that could affect the bearing’s performance.
- Inspect the bearing: Before installation, carefully examine the bearing for any signs of damage or defects. If any issues are detected, replace the bearing.
- Choose the right tools: Always use the proper tools and equipment for installing bearings. This includes tools specifically designed for bearing installation to prevent any damage.
- Apply lubrication: Apply the appropriate amount of lubrication to the bearing and its mating surfaces. This helps reduce friction and ensures smooth operation.
- Align the bearing: Proper alignment is crucial for the bearing’s performance. Ensure that the bearing is aligned correctly with the shaft or housing using precision measuring tools if necessary.
- Apply the correct pressure: Use a suitable press or mounting tool to apply the correct amount of pressure during installation. Avoid excessive force that could damage the bearing.
- Secure the bearing: Once the bearing is properly installed, secure it in place using the recommended locking mechanism, such as retaining rings or locking nuts.
Avoiding Common Installation Errors
Common installation errors can lead to premature bearing failure. To avoid these issues, keep the following points in mind:
- Avoid hammering or using excessive force during installation, as it can cause damage to the bearing and its components.
- Ensure that the bearing is not subjected to misalignment, as it can lead to increased wear and reduced performance.
- Do not preheat or overheat the bearing, as it can alter its properties and compromise its functionality.
- Always follow the manufacturer’s guidelines and recommendations for installation, including torque specifications and tightening sequences.
- Regularly inspect the installed bearings for any signs of damage or wear, and address any issues promptly.
By following correct installation techniques and avoiding common errors, you can maximize the lifespan and performance of your bearings. Taking the time to install bearings properly will contribute to the reliability, productivity, and overall operating costs of your equipment.

Credit: tractian.com
Lubrication Strategies
Proper lubrication is essential for maintaining the performance and longevity of bearings. Choosing the right lubricant and following appropriate lubrication schedules and techniques are crucial aspects of bearing maintenance. In this section, we will explore the key considerations for effective lubrication strategies.
Choosing The Right Lubricant
When it comes to selecting the right lubricant for your bearings, it is important to consider factors such as operating conditions, load, speed, and temperature. The lubricant should have the necessary properties to reduce friction, prevent wear, and protect against corrosion.
Here are some key points to keep in mind when choosing a lubricant:
- Identify the specific requirements of your application and consult the manufacturer’s recommendations.
- Consider the viscosity and consistency of the lubricant, as it affects the film formation and ability to withstand different operating conditions.
- Ensure compatibility between the lubricant and the bearing materials to avoid any potential chemical reactions.
- Take into account the potential for contamination and select a lubricant that provides adequate protection against contaminants.
Lubrication Schedules And Techniques
Establishing proper lubrication schedules and techniques is essential for maintaining optimal bearing performance. Regular lubrication helps to reduce friction, dissipate heat, and prevent premature wear and failure.
Consider the following guidelines when developing lubrication schedules and techniques:
- Refer to the manufacturer’s recommendations for the recommended lubrication interval and quantity.
- Take into account the operating conditions and adjust the lubrication frequency accordingly, especially in demanding environments.
- Ensure cleanliness during the lubrication process to prevent the introduction of contaminants.
- Use the appropriate lubrication method, such as manual greasing, automatic lubrication systems, or centralized lubrication systems, based on the application requirements.
- Monitor the lubricant condition regularly and perform oil analysis or grease sampling to detect any signs of degradation or contamination.
By following these lubrication strategies, you can significantly enhance the performance, reliability, and lifespan of your bearings, reducing downtime and maintenance costs.
Aligning And Mounting Bearings
Proper alignment and secure mounting of bearings are crucial for optimal performance and longevity. In this section, we will delve into the importance of alignment and mounting in bearing maintenance.
Alignment For Optimal Performance
Correct alignment of bearings ensures smooth operation and prevents premature wear. Misalignment can lead to increased friction and stress on the bearings, reducing their lifespan.
Secure Mounting To Prevent Movement
Securely mounting bearings is essential to prevent movement that can cause noise, vibration, and even bearing failure. Proper mounting reduces the risk of misalignment and ensures efficient operation.
Troubleshooting Bearing Problems
When it comes to maintaining industrial equipment, dealing with bearing problems is a common challenge. Timely detection and resolution of bearing issues are crucial for preventing costly downtime and equipment damage. In this section, we will delve into the key aspects of troubleshooting bearing problems, focusing on diagnosing unusual bearing noises, and addressing excessive vibration and heat.
Diagnosing Unusual Bearing Noises
Unusual bearing noises can be an early indication of potential problems. By carefully listening to the sounds emitted by the bearings, you can identify issues and take corrective measures. Here are some common abnormal bearing noises:
- Grinding
- Squeaking
- Rumbling
- Clicking
Regular monitoring of these noises can help in early detection of problems and prevent further damage.
Addressing Excessive Vibration And Heat
Excessive vibration and heat are red flags indicating potential bearing issues. The following steps can help in addressing these problems:
- Ensure proper lubrication to reduce friction and heat buildup.
- Inspect for misalignment and imbalance, which can contribute to excessive vibration.
- Check for proper installation and mounting of bearings to minimize vibration.
- Monitor temperature levels using thermal imaging to detect overheating.
Prompt action to address excessive vibration and heat can prevent premature bearing failure and extend the lifespan of equipment.
Advanced Maintenance Tools And Equipment
When it comes to bearing maintenance, having advanced tools and equipment is crucial for ensuring optimal performance and longevity. The use of cutting-edge maintenance tools and technology not only simplifies the maintenance process but also helps in monitoring the health of the bearings effectively.
Must-have Tools For Bearing Maintenance
Proper maintenance of bearings requires the use of essential tools to facilitate inspection, installation, and lubrication. Below are the must-have tools for effective bearing maintenance:
- Bearing Pullers: Essential for removing bearings from shafts and housings without causing damage.
- Hydraulic Fitting Tools: Used for precise and efficient fitting of bearings onto shafts.
- Grease Pumps: Facilitate the accurate dispensing of lubricants to ensure proper lubrication of bearings.
- Vibration Monitoring Equipment: Enables the early detection of potential bearing issues through vibration analysis.
- Ultrasonic Testing Devices: Utilized for detecting early signs of bearing failure by analyzing ultrasonic emissions.
Using Technology To Monitor Bearing Health
Technology plays a vital role in monitoring the health of bearings and identifying potential issues before they escalate. With the use of advanced monitoring equipment and technology, it becomes possible to proactively assess the condition of bearings and take preventive measures to avoid unexpected failures.

Credit: www.researchgate.net
Preventative Measures And Best Practices
To prevent bearing problems, follow these best practices for maintenance: handle with care, check housing and shaft, mount correctly, avoid overheating, use proper tools, prevent corrosion, and ensure proper lubrication. Regular maintenance and inspection can avoid many bearing issues, improving reliability and reducing operating costs.
Strategies To Extend Bearing Life
Bearings are an essential component of various machines and equipment, and it is crucial to ensure their proper functioning. One of the best ways to extend the life of bearings is to implement strategies that can prevent damage and wear. These strategies include using the correct lubrication, maintaining the proper alignment and clearance, and avoiding overloading. Additionally, ensuring that the bearings are installed correctly can go a long way in preventing premature wear and tear.Creating A Preventative Maintenance Schedule
Another best practice for bearing maintenance is to create a preventative maintenance schedule. This schedule should include regular inspections and maintenance activities to ensure that the bearings are in good condition. The maintenance schedule should also specify the type of lubrication and the frequency of lubrication for each bearing. By implementing a preventative maintenance schedule, you can identify and address any potential issues before they become severe problems.Best Practices For Bearing Maintenance
To ensure that your bearings operate at peak performance, it is essential to follow some best practices for bearing maintenance. These include:- Regularly inspecting the bearings for any signs of wear or damage
- Cleaning the bearings thoroughly before re-lubricating them
- Choosing the right lubricant for the specific application
- Properly storing bearings when not in use
- Using the correct tools for installation and removal
- Maintaining the proper clearance and alignment
Case Studies: Bearing Failures And Fixes
Explore real-world solutions for bearing problems and maintenance through insightful case studies on bearing failures and effective fixes. Discover practical tips and expert advice to ensure optimal bearing performance and longevity.
Real-world Bearing Problem Scenarios
Let’s delve into real-life scenarios that showcase bearing failures and their solutions.
Lessons Learned From Bearing Maintenance
Discover valuable insights gained from bearing maintenance practices.
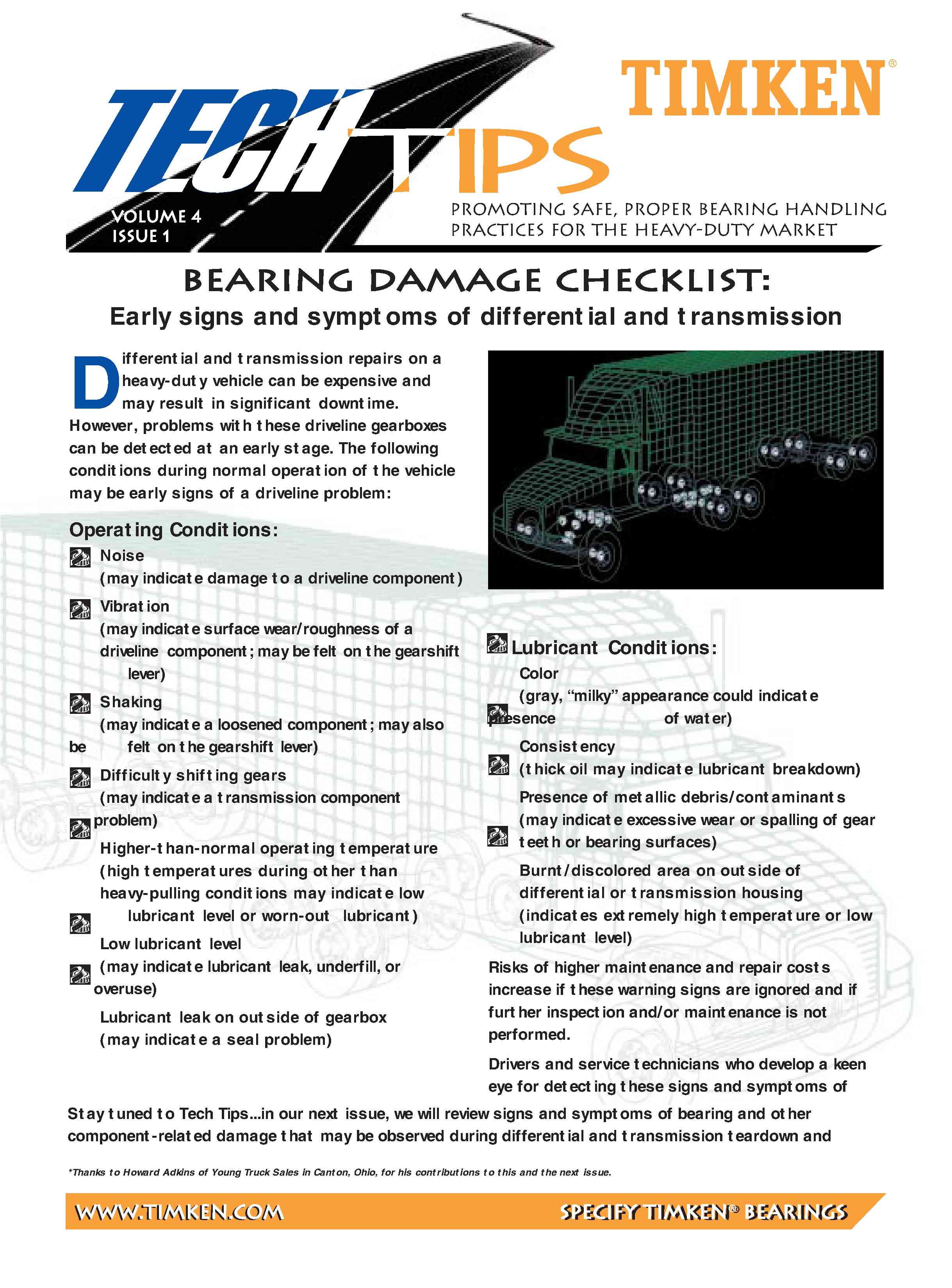
Credit: www.dtcomponents.com
Conclusion: Maximizing Bearing Efficiency
Maximizing bearing efficiency requires proper maintenance and inspection to avoid common problems such as overheating, contamination, inadequate lubrication, misalignment, corrosion, and bad fits. Handle bearings with care, check housing and shaft, mount them correctly, use proper tools, avoid corrosion, and ensure proper lubrication for a longer lifespan.
Summarizing Key Maintenance Tips
Proper bearing maintenance is crucial for ensuring optimal performance and longevity. By handling bearings with care, checking housing and shaft conditions, and using the correct tools, you can prevent damage and extend the lifespan of your bearings. Additionally, avoiding preheating, overheating, and corrosion, while ensuring proper lubrication, are key steps in maintaining bearing efficiency.
Adopting A Proactive Approach To Bearing Care
Adopting a proactive approach to bearing care involves regular inspections and maintenance to identify and address potential issues before they escalate. Monitoring for warning signs such as squeaking, grinding noises, excessive vibration, and fatigue can help prevent bearing failure and minimize downtime. By addressing common failure factors like overheating, contamination, inadequate lubrication, misalignment, and corrosion, you can proactively safeguard your bearings against damage.
Frequently Asked Questions
What Is The Basic Maintenance Procedure For A Bearing?
To maintain a bearing, handle with care, check housing and shaft, mount correctly, avoid overheating, use proper tools, and prevent corrosion. Proper maintenance and inspection can avoid many problems and improve reliability and operating costs.
What Are The Warning Signs Of A Bearing Failure?
The warning signs of bearing failure include squeaking, grinding noises, excessive vibration, and increased fatigue rate. These indicators shorten the bearing’s service life and should prompt immediate inspection. Regular maintenance and proper handling can prevent many bearing problems and improve equipment reliability.
Do Bearings Need Maintenance?
Bearings require maintenance to ensure their optimal performance and longevity. Here are some essential tips for bearing maintenance: handle them delicately, check the housing and shaft, mount them correctly, avoid overheating, use proper tools, prevent corrosion, and ensure proper lubrication.
By following these procedures, you can avoid many bearing problems and enhance the reliability, productivity, and operational costs of equipment containing bearings.
What Is The Most Common Bearing Failure?
The most common bearing failure types include overheating, contamination, inadequate lubrication, misalignment, corrosion, brinelling, electrical pitting, improper mounting, and bad fits.
Conclusion
Proper maintenance is crucial to prevent bearing problems and ensure a longer lifespan. By handling with care, checking housing and shaft, mounting correctly, using proper tools, and ensuring proper lubrication, many issues can be avoided. Regular inspection and maintenance can improve reliability, productivity, and operating costs for equipment containing bearings.